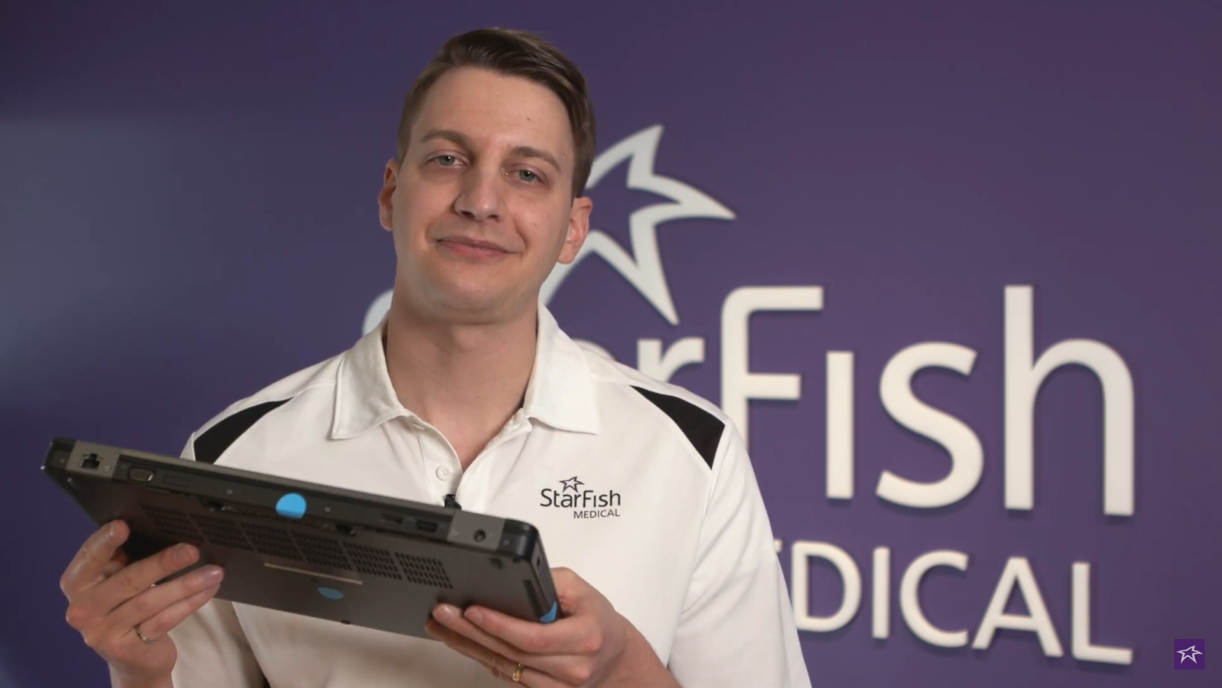
How to Perform Medical Device Drop Test
Medical Device Drop Test and Push Test are part of IEC 60601-1 and common in medical device product design & development projects. This blog describes two of the most common mechanical tests that medical device designers may want to perform in-house before sending a device for third party testing.
If you’re trying to market an electronic medical device in the EU, Canada, the USA, or other regions that recognize IEC 60601-1 then you will need to ensure your device complies with 60601-1. Certification testing to 60601-1 must typically be completed formally by a third party laboratory before a device can be approved for sale. However, formal third party testing can take weeks or even months, and if there is a design issue or failure that needs to be resolved, it can take even longer.
Experienced engineers designing a medical device will often test their device in house first to increase confidence it will pass the formal testing regime later and to resolve any design issues quickly, thus reducing overall effort and schedule.
What is the Drop Test for and is my specific device in scope?
The drop test ensures that your device is resistant to stress caused by free fall.
This particular test applies to all portable mobility classifications of medical electrical devices, including body worn and handheld devices, and accessories or relevant parts of non-portable equipment.
How do I Test a Body Worn or Handheld Device, or Accessory?
This testing is performed per Clause 15.3.4.1. If you haven’t checked out the video, have a look to see these step by step instructions in action:
- Depending on your device, determine the three most likely orientations for it to be dropped during normal use
- For example, upright, on the left side, and upside down
- Chose auxiliary locations if needed
- If your product risk profile indicates the need, consider testing additional orientations that may result in risk
- Place a 50 mm +/- 5 mm thick hardwood board on a concrete surface that is wide enough to fit the device
- Make a mark 1 m above the top of the hardwood board using a calibrated measure device
- Holding the device by hand, or with mechanical gripper, hold the device at or just above the 1 m mark. If performing the test by hand, try not to throw it up or down. Simply allow the device to free fall by dropping it from one of the orientations onto the hardwood board
- Repeat the test once again for the second and once again for the third orientations
- Review and/or test your device afterwards for unacceptable risk, which might mean any or all of the following (or more):
- Visually looking for sharp or broken edges
- Performing ingress protection tests, dielectric strength tests, leakage tests, etc.
- Confirming that creepage or clearance distances are still maintained
- Operating the device and verifying essential performance is maintained
- Additional tests might be conducted following the drops
How do I Test a Portable Device that isn’t Body Worn or Handheld?
This testing is done per Clause 15.3.4.2. If you haven’t checked out the video, have a look to see these step by step instructions in action:
- Determine all the orientations in which the device can be placed on the working surface during normal use. For many devices, that may be a single orientation
- For example, a toaster may only be placed upright in normal use
- Choose auxiliary locations if needed
- If your product risk profile indicates the need, consider testing additional orientations that may result in risk
- Place a 50 mm +/- 5 mm thick hardwood board on a concrete surface
- Make a mark 5 cm, 3 cm, or 2 cm above the top of the hardwood board depending on if your device is less than 10 kg, between 10 kg and 50 kg, or greater than 50 kg, respectively
- Holding the device by hand, or with fixed gripper, hold the device at, or just above, the height mark made in the previous step. If performing the test by hand, try not to throw it up or down. Simply allow the device to free fall by dropping it from one of the orientations onto the hardwood board
- Repeat the test two additional times in the same orientation
- If you have identified additional orientations, repeat the two steps above for each one, resulting in three total drops in each orientation
- Review and/or test your device afterwards for unacceptable risk, which might mean any or all of the following (or more):
- Visually looking for sharp or broken edges
- Performing ingress protection tests, dielectric strength tests, leakage tests, etc.
- Confirming that creepage or clearance distances are still maintained
- Operating the device and verifying essential performance is maintained
- Additional tests might be conducted following the application drops
What is the Push Test for and is my specific device in scope?
The push test ensures that your device is sufficiently rigid to protect against unacceptable risk.
This particular test applies to all mobility classifications of medical electrical devices, so if 60601-1 is in scope, then this test is also in scope.
How do I do it?
If you haven’t checked out the video, have a look to see these step by step instructions in action:
- Choose a location on each part of your external enclosure to test
- For example, if your device has three plastic parts and one LED display that make up the outside of the enclosure, then each of the three plastic parts need to be tested. The LED display is out of scope per Clause 15.3.1
- If your device is over 18kg, then the bottom does not need to be tested
- Choose auxiliary locations if needed
- If your product risk profile indicates the need, consider testing additional locations such as seams, buttons, etc.
- Place your device on a working surface such as a table, and brace as necessary to ensure it won’t slide or fall over during testing
- Prepare a calibrated force gauge with a 30mm circular tip
- Don’t have a force gauge? You can use a 25kg weight to test the top surface, but the side surfaces might be trickier, as simply turning the device on its side might not be fully representative for the expected loading depending on the device design and complexity
- Apply 250N +/-10N of force to each chosen location for at least 5 seconds
- Review and/or test your device afterwards for unacceptable risk, which might mean any or all of the following (or more):
- Visually looking for sharp or broken edges
- Performing ingress protection tests, dielectric strength tests, leakage tests, etc.
- Confirming that creepage or clearance distances are still maintained
- Operating the device and verifying essential performance is maintained
- Additional tests might be conducted following the application of the force
What if the device fails?
If your device fails, and if you’re confident you performed the test correctly, you may need to revise the design of your device to improve its drop or push resistance and retest.
What if it passes?
If the device passes, then you can have additional confidence that the device will pass formal third party testing.
Are any other tests needed? And if so, what order do I do them in?
It is almost certain that more tests will be needed for 60601-1 testing. The order of testing isn’t prescribed by the standard – it’s up to the test engineer to determine if it makes sense to perform all (or sets of) tests on the same sample or not. The same applies to which order and what types of inspection to do in between tests. Analogues can also be useful in certain situations. The thing to remember is that all tests within a clause should be performed immediately one after the other without modifying or repairing the device in any way (i.e., if a device becomes damaged during testing, don’t fix the issue and continue testing. Instead, fix the issue and restart the test(s) from the beginning).
Anything else?
That’s it! As you can see these tests are not that onerous to setup and perform, but are definitely worth completing in-house before formal testing by a third party. If you have a high-frame rate camera, use it to help identify failure points (and make cool slow-mo shots too). Happy testing!
Image: StarFish Medical
Nigel Syrotuck is a StarFish Medical Team Lead Mechanical Engineer and frequent guest blogger for medical device media including MD+DI, Medical Product Outsourcing, and Medtech Intelligence. He works on projects big and small and blogs on everything in-between.
Another key requirement for ISO 60601-1 is the protection against ingress. Read more here.