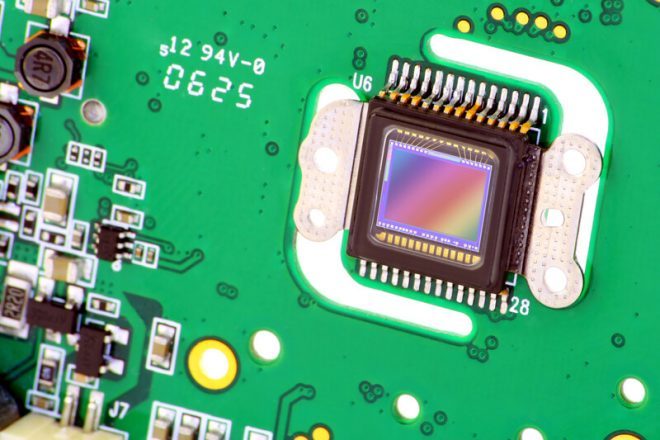
PCB Design Best Practices Pt. 2
Last week I shared ideas, tips and suggestions that I believe increase the chances of being successful when designing printed circuit boards. Here’s a few more that come to mind.
The output files for PCBs are still in the old Gerber format. These files never contain quite enough information to be sure the boards will turn out right. For instance they don’t contain units and often even the decimal place is ambiguous. When I generate the output files I always turn off zero suppression and I always use an absolute origin, both for the Gerbers and the drill files.
It’s so common to have either a scaling or offset error between all the files. I also insist that all Gerbers are inspected using a viewer that is not the EDA package that generated them. Maybe it’s just superstition but it also often catches issues. There are a number of things I consider when laying out switch-mode power supplies or filters on PWM circuits like H-bridges. Mostly I think about the high frequency current paths – there are usually two of them – and keep the area of these paths minimized. This usually means placing the big components first: switches, inductors, caps and diodes.
I only connect switch-mode supply and PWM filter circuits to the rest of the PCB ground in one place. This includes signal grounds to the control ICs. I generally use the ground terminal of the main input capacitor. If the connection is done in more than one location, the ground plane and hence other circuits may be polluted with switching currents. Be wary of nearby copper pours accidentally touching the ground net somewhere else.
One thing I do every time is to simulate the inductor currents at worst case conditions: max current, min inductance, max input voltage, etc. I do this to determine the peak inductor current; it’s often way higher than you might expect. It can be checked analytically of course but personally I find simulation effective. The peak current should be reasonably below the saturation current of the inductor. Remember the effective inductance drops with current as the core saturates. This should be accounted for in your simulation. This time is never wasted.
Given that medical devices are heavily regulated, at some point electromagnetic compatibility will have to be considered. I now add ESD & EMC reduction components like TVS diodes and ferrites, even if I’m not planning to do any EMC testing on the board. Partly I like to get a head start to flush out problems early; partly it often happens that a prototype ends up being used beyond what was initially imagined or intended. Often I’ll design in the parts but won’t bother populating them right away. At least they can be easily added later if required without cutting and gluing.
I consider where noise may come from both on the PCB and off it. It’s always better to nip the noise at the bud rather than trying to fix it wherever it ends up causing trouble. An example of this is the high speed parallel lines to a TFT display. A tidy bank of ferrites right at the driver outputs is often all it needs. Of course this is easiest done at the PCB design stage.
Pretty much every PCB in every piece of equipment I work on is heavily influenced and constrained by the work of other disciplines. In fact it’s really rare that a board can be designed without heavy consultation throughout the design cycle with mechanical engineers or industrial designers. I find there is no clear owner to the mechanical constraints of a PCB. Often I’ll propose a board outline; this will then get squooshed and munched as the housing design gets hashed out; then I’ll rearrange it as the main, large components, connectors and things get roughly placed; then this will be tweaked again by the MEs or IDs and lastly I’ll do the final touches and throw it back. This process is highly iterative and relies more and more on accurate 3D modeling of the board as well as connectors and wiring. For more of my thoughts on wires, check out my previous blog “I hate wires”.
I like to keep in mind that PCBs are structural elements with all sorts of great mechanical properties: they are fairly rigid, they’re pretty strong and their tolerances are often excellent. The collaboration doesn’t stop there either. Whoever is doing firmware, software and logic design will also have some strong opinions about the board. It’s best to all get together early and often to minimize the chance of later rework or worse.
These are some of the PCB design strategies that I use to increase the chances that the boards are useful. I would be happy to hear any of your tips and strategies too.
Kenneth MacCallum, PEng, is a former Principal Engineering Physicist at Starfish Medical. He works on Medical Device Development and designs PCBs in Digital Health and ultrasound applications.
Images: StarFish Medical