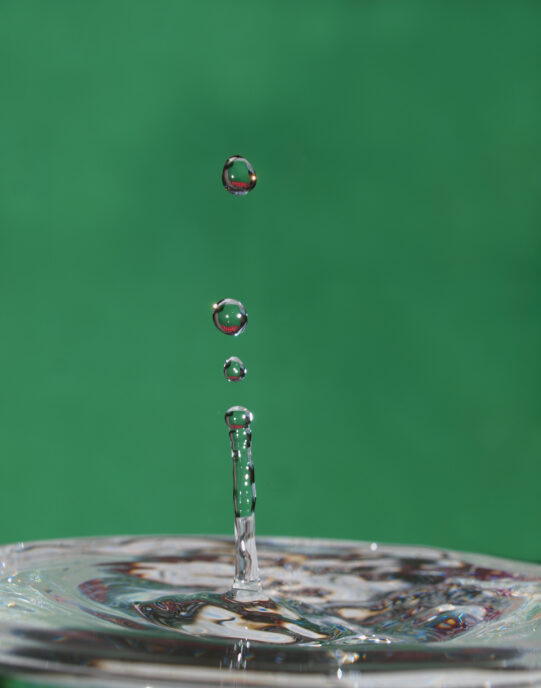
The Usefulness of Computational Fluid Dynamics in Medical Device Design
First principles calculations are the best way to give a design concept a reality check and worthy fluid dynamics books have a wealth of reference information on drag coefficients, major/minor losses, hydraulic diameter calculations, and a trusty Moody diagram. However, sometimes the problem is less intuitive…
For example, non-Newtonian fluid flow, actual flow from a fan, or convective heat transfer coefficients around unusual geometries or flow conditions. Another example of non-intuitive flow calculation involves non-standard inlet conditions, where the losses are a blurry combination of coefficients. In these instances, the actual pressure, flow, or temperature experienced can be calculated, but typically requires iteration and simplifications that may not accurately reflect reality.
In order to gain insight into unique, but simplifiable fluidics problems, computational fluid dynamics can be utilized. Early stage CAD modeling can be leveraged to conduct simple CFD calculations. Want to know if your fan is going to be 50% larger because of the addition of a low permeability mesh or porous media placed on the outlet of an enclosure for ingress protection? Will the outside of an enclosure adhere to 60601 temperature requirements for contact with human skin? Is it possible to passively cool an electronic component to less than 70C?
Answers to these questions are possible with CFD. The steps involved are as follows:
1. Check suitability of CFD and conduct quick first principles calculations
2. Import or generate a simplified CAD model
3. Check and correct model surfaces/gaps/etc
4. Define model solid and fluid properties
5. Create inlet and outlet boundary conditions (fans, heat sources, isotherms, etc)
6. Create appropriate convergence goals
7. Mesh Refinement
8. Post analysis
In a recent project, a pseudoplastic fluid was to be extruded through an irregular orifice with a known inlet pressure. What was not known was the size of orifice that was needed for a desired flow rate. The interdependencies of the variables (shear rate, viscosity, and orifice size/geometry) favored a CFD analysis. The rheologic curve was inserted as a custom fluid and a solid model with a series of holes of different sizes was created. The final analysis indicated we were in the right ballpark for sizing and provided confidence that a physical system would work, prior to cutting any materials. This simplified and cost effective de-risking activity would not have been easy to conduct with hand calculations.
An additional side benefit of conducting CFD analysis is the ease of leveraging the output data for distribution. Post analysis can produce enlightening animations of flow paths, isotherms, inlet pressures, etc. This data can be packaged in videos and images for distributing knowledge to a development team as well as for marketing / investor collateral.
Mark Drlik is the StarFish Medical Concept Development Manager. He created the cool looking medical device CFD simulations (image and movie clip) for this article.
Image: freeimages.com