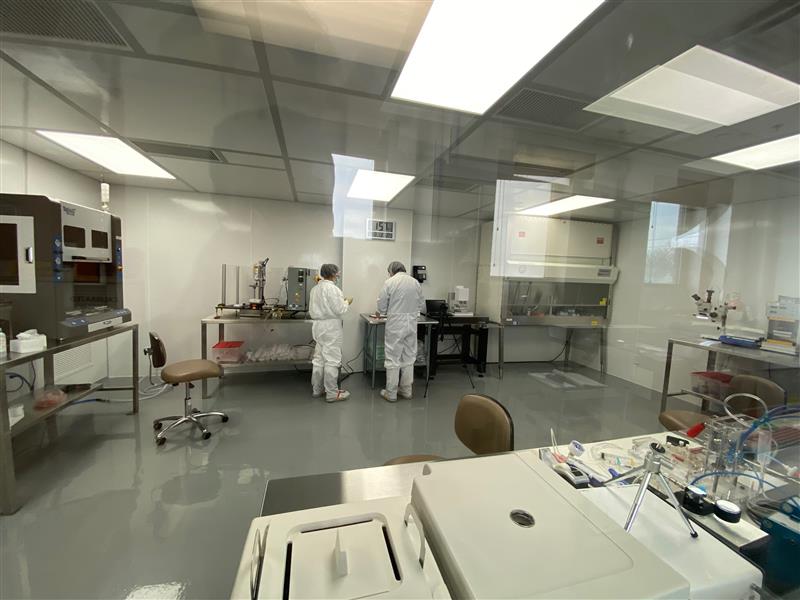
Cleanroom Validation Testing for Medical Device Manufacturing
This overview of Cleanroom Validation Testing for Medical Device Manufacturing draws upon our experience validating a Class 7 Cleanroom.
A highly regulated environment, like that of a ISO 13485:2016 certified medical device manufacturer, requires assurance that critical processes can be performed within a controlled environment.
Cleanrooms control and maintain a stable manufacturing environment for products that require little to no contamination from external material.
The Basics of Cleanroom Validation Testing
When you think of cleanrooms, you usually think of a closed off white room with people dressed in gowns a wearing mask, and gloves doing R&D or manufacturing. For the most part that is correct.
Cleanroom is a pretty broad term, but generally it just means a room that is cleaner than a regular room. They are kept clean using a variety of filters in a pressurized room, consistent temperature and the individuals who work in them wear protective clothing to prevent contaminating the room with foreign particulates.
The ISO 14644-1 defines the class of cleanliness required by manufacturers and the tasks associated with process validation.
Cleanroom classes range from ISO 1 to ISO 9. ISO 1 being the “cleanest” class and ISO 9 is the “dirtiest” class. Even if it’s classified as the “dirtiest” class, the ISO 9 clean room environment is again cleaner than a regular room.
The most common ISO clean room classes are ISO 7 and ISO 8;
ISO 7 | 30–60 air changes per hour and maintains air cleanliness levels of a maximum of 10,000 particles
ISO 8 | 15–25 air changes per hour (ante-room) and maintains air cleanliness levels of maximum of 100,000 particles
Building and Validating our Toronto Cleanroom
Cleanrooms can be an expensive investment for a manufacturer. They must be customizable to produce specific products that are subject to special requirements that require a controlled environment to minimize contamination.
Cleanroom Validation Testing for our Toronto site is an ISO 7 certified room with a gowning area that is certified at ISO 8. We regularly monitor the pressure, particle count and replace HEPA filters as needed to maintain these levels of cleanliness.
When building a cleanroom, it is important to design it correctly from the start. This ensures all requirements are met early on as changes can be more costly and timely.
During the installation of the Cleanroom in our Toronto office we conducted the following tests to validate the cleanliness of our cleanroom.
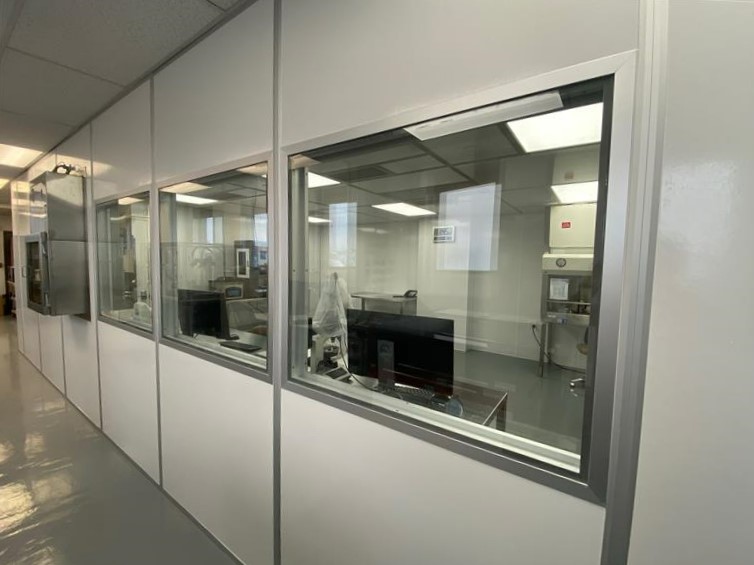
HEPA Validation and Cleanroom Validation Testing
H.E.P.A. (High Efficiency Particulate Air) filters are the primary component requiring validation in a cleanroom. Validation is conducted through a filter integrity test. H.E.P.A. filters are made out of a boron silicate microfibre manufactured paper. It is a very delicate material and is very susceptible to either physical damage or leaks due to wear and tear from pressures and stresses caused by daily operation in the cleanroom. The particle sizes that H.E.P.A. filters are designed to trap are very small, and even small holes in the filter or leaks on the gaskets, frame, or seals can cause substantial damage to products being worked on within the cleanroom.
A H.E.P.A. filter leak test is important to pinpoint and correct H.E.P.A. filter performance problems before they can escalate to a point where they cost the user both time and money on failed experiments or projects. These filters should also be replaced periodically to ensure the room maintains its specified level of cleanliness.
Air Flow Validation
An Air flow test in cleanrooms is as important as the filter integrity tests. Verifying the air flow (velocity, volumetric flow, directional flow, refluxing etc.) ensures that adequate flow of unidirectional air (“laminar flow”) or non-unidirectional flow for the purpose of particle dilution is being achieved in the cleanroom. Also, cleanroom users should have assurance that air flow is directionally controlled, or that air flow is not being deflected or redistributed to areas of the cleanroom where contamination can result from air flow problems including air current refluxing, dead spots, or turbulence.
Particle count validation
Particle count tests should be performed within the cleanroom when it is at full operational status to determine the actual number of airborne particles generated and present while the cleanroom is being used. Testing should include sampling of airborne particles at several different particle size ranges, to adequately determine a profile of the particle distribution. Testing should also include artificially generated particles [see photo 1] and ambient testing during use. Regularly scheduled particle count tests should be performed to ensure that particle count is within the specified range of the cleanroom. This can be done with a particle counter at different locations in the cleanroom.
Pressure validation
Cleanroom Validation Testing Enclosure pressurization testing should be performed as part of a periodic review. This will ensure that a proper pressure differential is being maintained. A great way to ensure the correct pressure is maintained is to have a Magnehelic pressure gauge present in the cleanroom and proper protocols to check if pressure is maintained before cleanroom activities. It is also important to make sure that the pressure gauge is calibrated at regular intervals specified by the manufacturer of the gauge. Any leaks in the cleanroom can result in an increase of unwanted particles entering the cleanroom and will decrease the cleanliness.
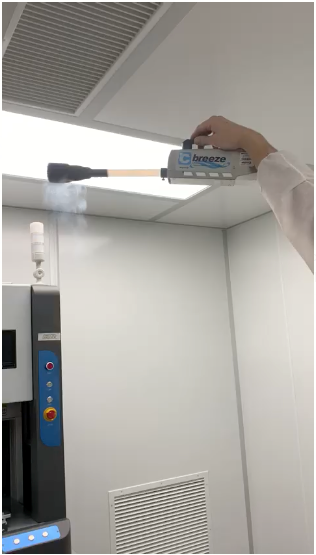
During our installation we found maintaining a consistent pressure and reducing leaks to be the most difficult part to maintain. I recommend addressing this early on in the design and assembly of the room. It is very difficult to adjust while validating and could be costly later on if you find areas or vents in the room where leaks are occurring.
In Summary
Cleanroom Validation Testing is an integral part of the production process in a variety of industries where product quality can be easily affected by outside factors such as temperature, pollutants, and air pressure. To reduce the risks of manufacturing errors and undesirable costs, validation testing of a cleanroom before use is key. This ensures that the manufacturing output is predicable, with little to no variation, and product specifications are met.
Images: StarFish Medical
Taimoor Khan is a QA/RA Specialist at StarFish Medical. Based in our Toronto office, Taimoor works on a variety of medical device projects. He follows his own advice on ROHS and REACH management and qualification regularly.