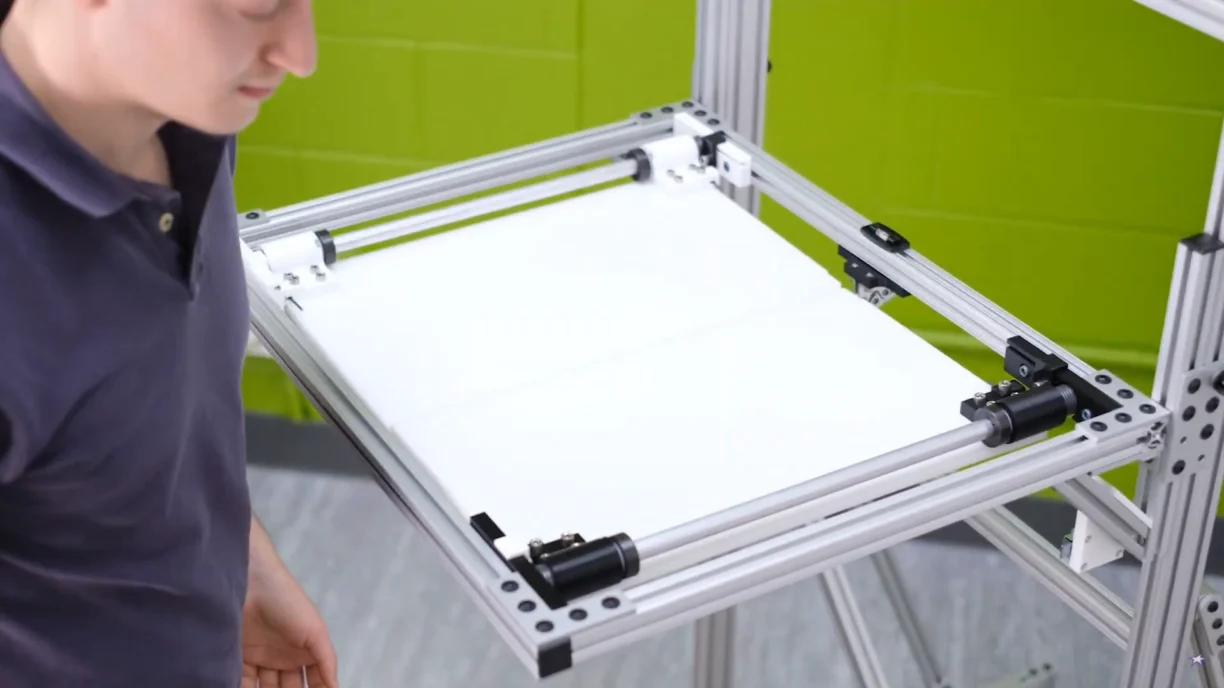
Medical Device Drop Testing in Action
Medical device drop testing helps ensure that products and packaging survive real-world handling. We demonstrate in-house drop testing on an actual device and its packaging using a custom-built drop tester.
From IEC Standards to Real-World Drops
While passing a standard test like IEC 60601-1 is a good first step, drop testing must also reflect real-world use. Devices get dropped repeatedly, often in uncontrolled settings. Packaging must protect the product all the way from warehouse to end user.
This episode shows how in-house testing setups let engineers explore failure modes before third-party verification. The drop tester featured includes adjustable doors, corner and edge supports, and surfaces for both hardwood and concrete impacts.
Testing Devices and Packaging
During testing, the team drops a medical device on various faces, edges, and corners. The results? Deformation, loose components, and internal rattling—clear signs of structural stress. Eventually, the device fails when dropped on its edge, offering valuable insights for redesign.
Next, they drop test a device package. Each face, edge, and corner is tested—including a downsized box for corner drop demos. A worst-case drop from double height shows whether the packaging holds up under extreme conditions.
Why In-House Drop Testing Matters
Medical device drop testing not only prepares teams for formal third-party tests but also helps identify weaknesses early. It saves time, protects users, and strengthens the final product. And yes—sometimes, it’s just fun to break things on purpose.
Related Resources
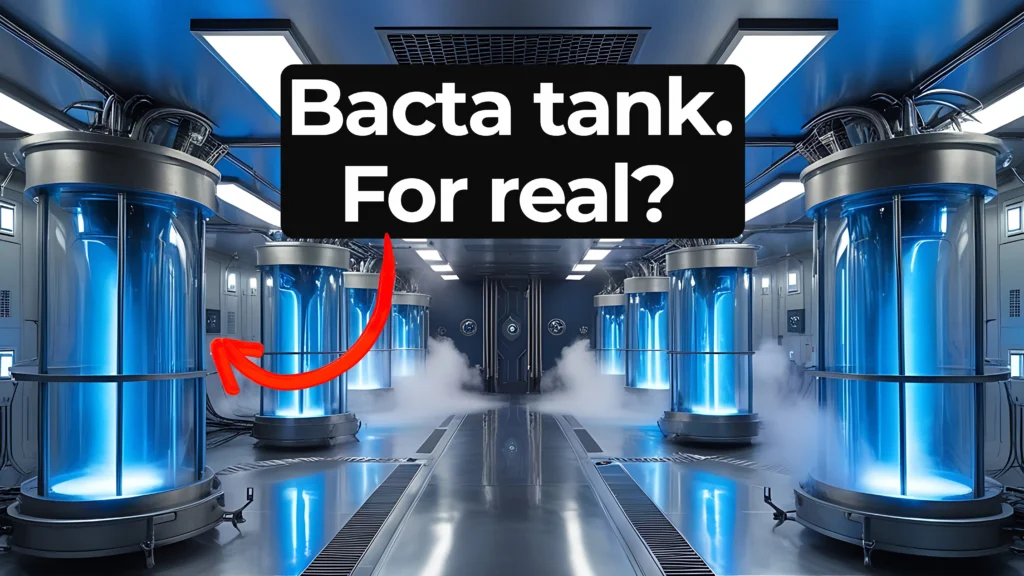
Ariana Wilson and Mark Drlik take inspiration from a scene in The Empire Strikes Back to talk about real-world parallels to the Star Wars bacta tank.
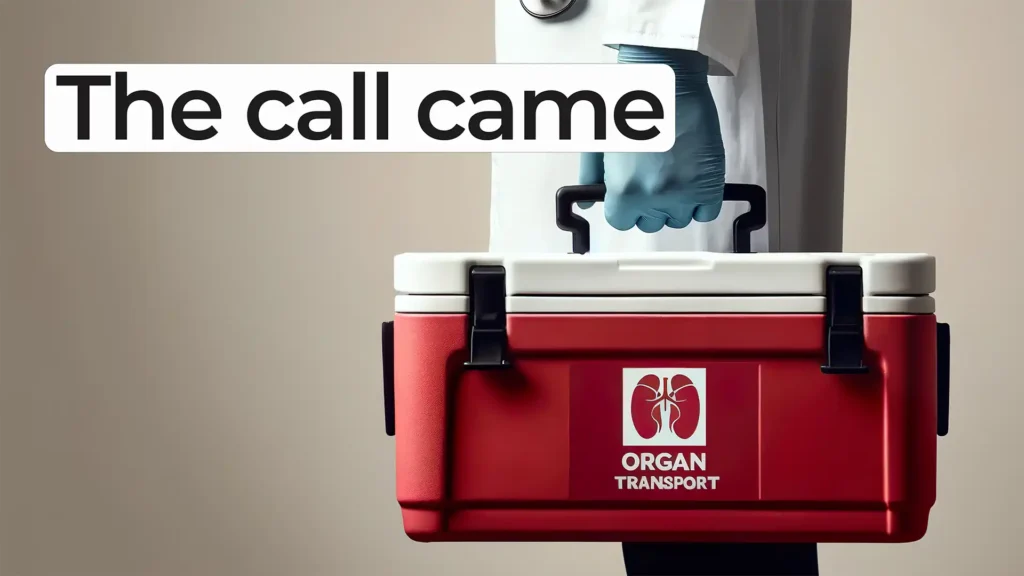
In this Before the Build episode, Eric Olson and Paul Charlebois dive into the importance of organ transplant logistics when designing effective medical devices.
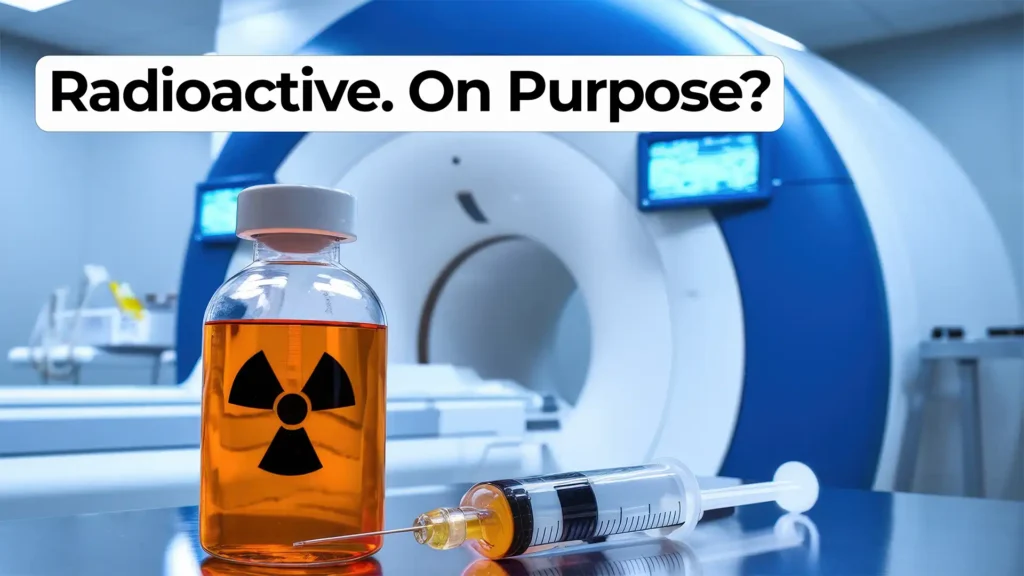
Radiopharmaceutical device development is gaining momentum as medical teams explore new frontiers in diagnostic imaging and cancer treatment.
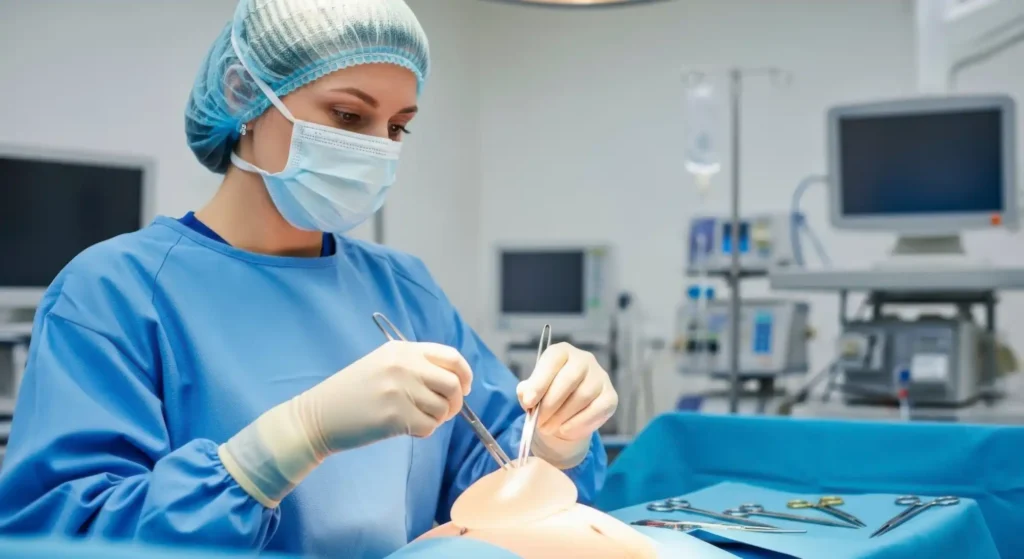
The simplest and least expensive way to train users of medical devices is to ask them study the Instructions for Use (IFU) beforehand.