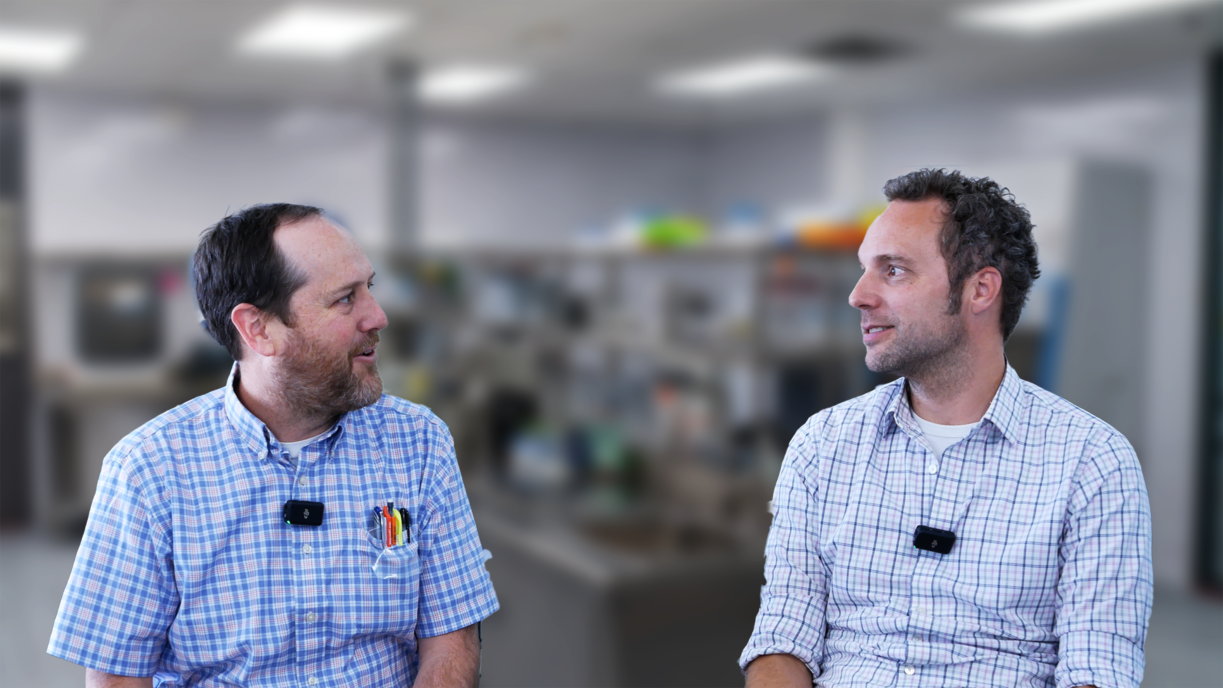
Bio Break: How much does it cost to develop a medical device?
What are the real costs of developing a medical device? In this episode of Bio Break, Nick and Joris dive into one of the most frequently asked questions they hear from clients: How much does it cost to develop a medical device?
When companies approach a product development firm like StarFish Medical, they usually bring a set of expectations around cost, timeline, and quality — what Nick calls the “holy trinity” of client expectations. But aligning these expectations with reality can be a challenge, especially for startups or first-time medical device entrepreneurs.
Nick and Joris explore what drives the cost of medical device development, from simple devices like tongue depressors to complex systems like MRI machines. They highlight that costs vary widely depending on the device type, how mature the technology is, and whether there are existing components to leverage.
For example, when a client already has a validated lab-developed test (LDT) and wants to turn it into a product like an ELISA kit or a lateral flow assay, the development cost can be relatively modest — potentially a few hundred thousand dollars. In contrast, developing entirely new technology — where the scientific principles haven’t been proven and significant technical uncertainties remain — requires larger teams and longer timelines, driving costs into the millions.
Joris also points out that leveraging off-the-shelf components and reusing existing technologies can help reduce costs, but when you’re inventing something truly novel, the cost of technical innovation quickly adds up.
Finally, they remind viewers that clinical trials, regulatory approvals, and manufacturing scale-up will introduce additional costs beyond early prototyping and design.
How much does it cost to develop a medical device?
Learn how StarFish Medical led a consortium that created a Ventilator 2.0 therapy device in record time.
Related Resources
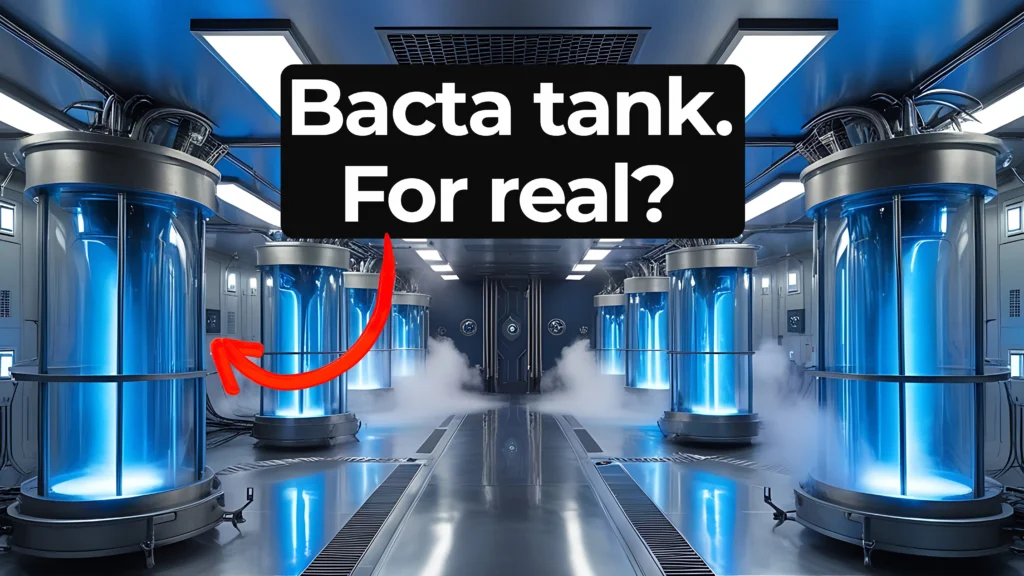
Ariana Wilson and Mark Drlik take inspiration from a scene in The Empire Strikes Back to talk about real-world parallels to the Star Wars bacta tank.
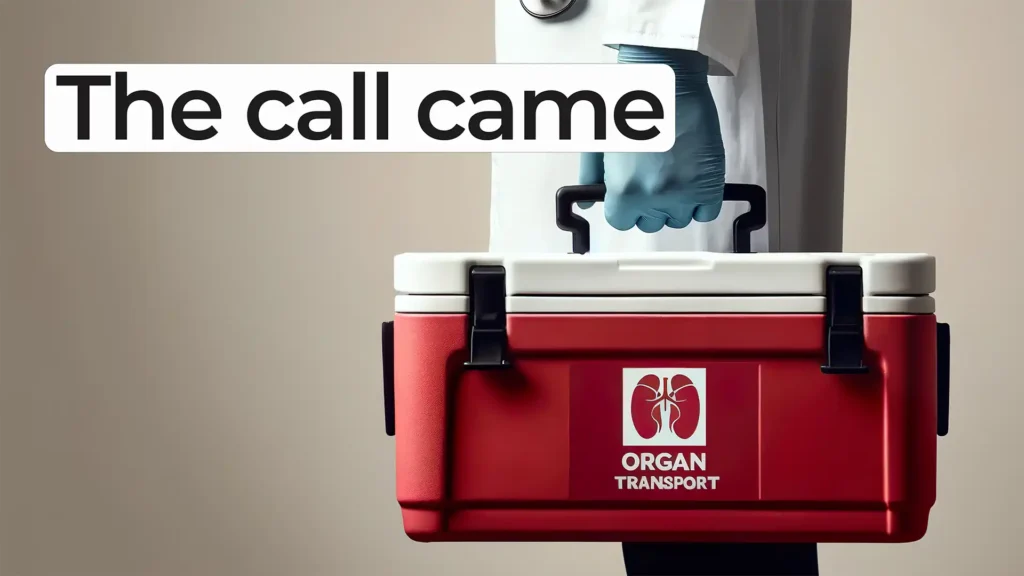
In this Before the Build episode, Eric Olson and Paul Charlebois dive into the importance of organ transplant logistics when designing effective medical devices.
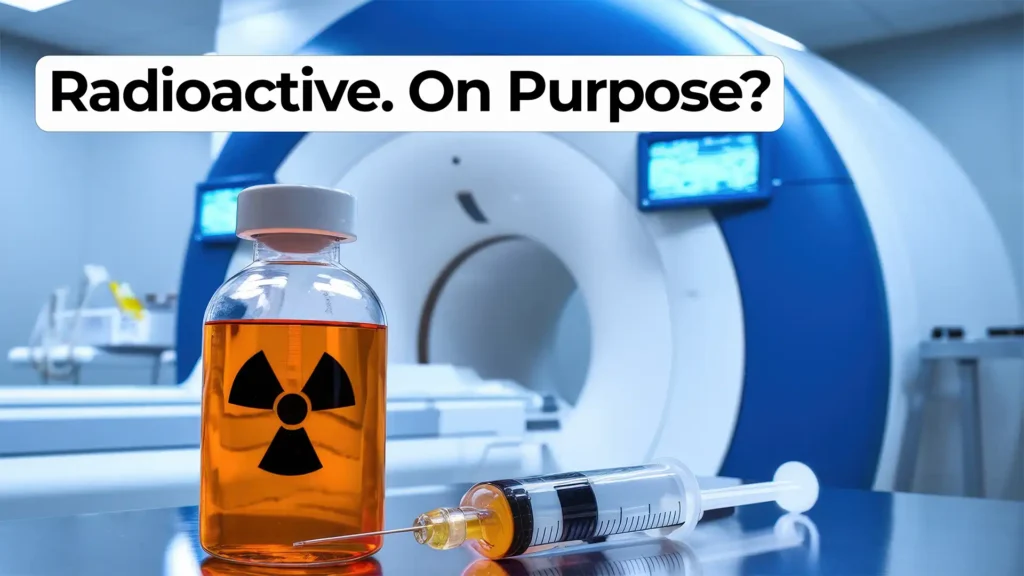
Radiopharmaceutical device development is gaining momentum as medical teams explore new frontiers in diagnostic imaging and cancer treatment.
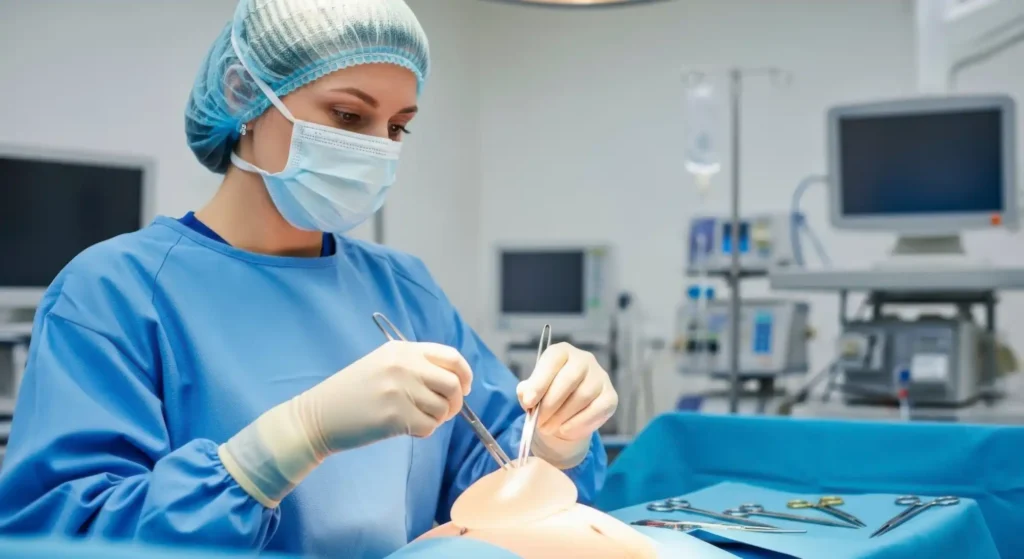
The simplest and least expensive way to train users of medical devices is to ask them study the Instructions for Use (IFU) beforehand.